Sustainable Water Infrastructure Contacts
Pacific Southwest, Region 9
Serving: Arizona, California, Hawaii, Nevada, Pacific Islands, Tribal Nations
Water & Energy Efficiency by Sectors
Sustainable Water Infrastructure Quick Finder | ||||
---|---|---|---|---|
FundingGreen Jobs in the Water SectorLow Impact Development | Waste To Biogas Mapping ToolWater Conservation/EfficiencyWater-Energy Connection | Water Loss ControlWhy Sustainability? |
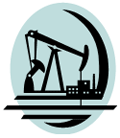
Oil Refineries
On this page:
- Energy
- Water
- Water and Energy Efficiency Case Studies in EPA Region 9
- Other Case Studies
- Get Recognition
EPA Programs & Resources
Additional Resources
- Energy Efficiency Roadmap for Petroleum Refineries in California, 2004 (PDF) (24pp, 1.3M) identifies petroleum industry issues, RD&D priorities, and options for increasing energy efficiency.
- Materials Research for Separation Technologies: Energy and Emission Reduction Opportunities, 2005 (PDF) (118pp, 2M)identifies opportunities for new and advanced materials in separation technologies that will lead to large reductions in energy use and harmful emissions.
You will need Adobe Reader to view some of the files on this page. See EPA's PDF page to learn more about PDF, and for a link to the free Adobe Reader.
How Can Water and Energy Be Used More Efficiently?
Oil refineries use a lot of water, and a lot of energy. Following a simple four step process (Benchmark, Audit, Implement, and Repeat), refineries can reduce their water and energy use. Such practices have economic and environmental benefits: they can save money, reduce climate impacts and lead to sustainability.
Energy
The U.S. petroleum refining industry is the largest in the world, providing 23 percent of world production and including inputs to virtually all economic sectors, including the transportation and the chemical manufacturing sectors. Significant quantities of energy are used to produce the petroleum products used by consumers and industry. The petroleum refining industry is one of the most energy-intensive manufacturing industries in the U.S. The industry used 3.1 quadrillion BTUs in 2002. The most energy-intensive refining processes include: distillation, hydrotreating, alkylation and reforming
For more of the latest environmental statistics and discussion on the Oil & Gas sector, see EPA’s 2008 Sector Performance Report.
Benchmark & Audit
When energy use isn’t being measured, it isn’t being managed. Quantifying the amount of energy being used is the first step toward evaluating where to cost-effectively improve energy efficiency. Learn about the benefits of proactively managing your plant’s energy use with ENERGY STAR’s Energy Strategy for the Road Ahead (PDF), 2007. (36pp, 618K)
Benchmarking services, tailored to complex refineries, are offered by consulting companies. Refineries can have their facility’s energy consumption benchmarked and compared to other refineries. ENERGY STAR provides a listing of commercial Service and Product providers.
Your benchmarking efforts can help identify one or more systems on which to focus an audit or assessment. A refinery energy audit can help identify specific projects to increase energy efficiency. Audits can either be facility-wide or focused on energy-intensive systems. A no-cost option is an Energy Assessment available through the Department of Energy’s (DOE) Save Energy Now program. Save Energy Now assessments primarily focus on energy-intensive systems: process heating, steam, compressed air, fans, and pumps.
EPA’s ENERGY STAR program offers a proven strategy for superior energy management with tools and resources to help each step of the way. To create momentum for energy performance improvements within individual manufacturing sectors, EPA organizes ENERGY STAR Industrial Focuses.ENERGY STAR provides a Focus for Refineries which includes an energy guide for plant managers in the petroleum refining industry (PDF) (122pp,715K).
Implement Efficiency Improvements
Implementing efficiency improvements is a site-specific process. The people in your organization can make or break your planned efficiency improvements. It’s important to obtain buy-in from key people at different levels of your organization. In addition, many refineries have internal “management of change” procedures to follow.
Participation in many of EPA’s and DOE’s voluntary energy efficiency programs gives refinery managers and staff access to networking opportunities with peers who have experience successfully implementing environmental management systems.In addition to EPA’s ENERGY STAR program and DOE’s Save Energy Now program, discussed above, there are several other voluntary programs which may be useful.
Combined heat and power (CHP), also known as cogeneration, is an efficient, clean, and reliable approach to generating power and thermal energy from a single fuel source.
The EPA’s Sector Strategies Program achieves performance improvement and burden reduction in 13 sectors by addressing their unique issues and challenges in a collaborative setting. Climate Leaders is an EPA industry-government partnership that works with companies to develop comprehensive climate change strategies.
EPA’s Green Power Partnership supports the organizational procurement of green power by offering expert advice, technical support, tools and resources.
Repeat
Repeating these steps allows for continual improvement.
Water
Significant quantities of water—primarily for processing and cooling— are needed to produce fuel. Refineries use about 1 to 2.5 gallons of water for every gallon of product, meaning that the United States, which refines nearly 800 million gallons of petroleum products per day, consumes about 1 to 2 billion gallons of water each day to produce fuel (USDOE, 2006).
Water used to be seen as a low-cost resource to refineries, and was used inefficiently. However, as the standards and costs for wastewater treatment increase and the costs for feedwater makeup increase, the industry has become more aware of water costs. In addition, large amounts of energy are used to process and move water through the refinery. Hence, water savings will lead to additional energy savings. (LBNL-55450, March 2004)
Benchmark & Audit
Also known as a water survey, a water audit is an excellent way to understand your current water use and future water savings. Generally, a water audit provides a detailed description of your facility’s water use, identifies potential water and financial savings, and recommends various water efficiency upgrades.
Your local water district or public utility may provide you with a free water audit. If not, you can hire a consultant to conduct a water audit.
Additionally, the WBCSD’s Global Water Tool is a free and easy-to-use tool for companies and organizations to map their water use and assess risks relative to their operations and supply chains.
Implement Efficiency Improvements
Renewable energy options—like solar, geothermal, and wind—use negligible amounts of water compared to conventional sources of energy (e.g. coal and nuclear); investing in renewables invests in water conservation!
When you use products bearing the WaterSense label in your kitchens, bathrooms and landscape, you can expect exceptional performance, savings on your water bills, and assurance that you are saving water for future generations. You can also save water by hiring certified water efficiency professionals, like WaterSense landscape irrigation professionals, Green Plumbers, and rainwater catchment professionals.
The EPA’s Green Infrastructure program has compiled information about various technologies & approaches, research, models & calculators, and case studies. You can save water and energy as well as improve water quality with green infrastructure.
Water Reuse, or water recycling, may offer your facility a tremendous water saving opportunity. EPA’s 2012 Guidelines for Water Reuse (PDF) (28pp, 372K) examines opportunities for substituting reclaimed water for potable water supplies where potable water quality is not required; it presents and summarizes recommended water reuse guidelines, along with supporting information.
Repeat
Repeating these steps allows for continual improvement.
Water and Energy Efficiency Case Studies in EPA Region 9
A petroleum refinery operated by ConocoPhillips in Billings, Montana is the first in the nation to earn the ENERGY STAR for superior energy performance. The refinery's design, operations and maintenance practices place the refinery in the top 25 percent of refineries nationwide in terms of energy efficiency.
BP’s Carson’s refinery (PDF) (6pp, 768K) produces 6 million gallons of gasoline a day. While the facility’s wells historically provided a sufficient quantity and quality of water, BP has needed to turn to another source: recycled water. As of 2007, 49% of the Carson refinery’s water is recycled water; by 2013, BP anticipates 90% will be recycled water.
Shell’s Martinez refinery (PDF) (2pp, 543K ) applied a systematic plant-wide assessment approach to identify energy and cost saving opportunities valued at $52 million in potential annual savings. Martinez Refinery factsheet (PDF) » (4pp, 240K)
Paramount’s refinery (PDF) (2pp, 543K ) applied a systematic plant-wide assessment approach to identify energy and cost saving opportunities valued at $4.1 million in potential annual savings.
Chevron’s Richmond refinery (PDF) (2pp, 115K) completed a motor system efficiency improvement project that resulted in $700,000 of annual savings.
Other Case Studies
- Installation of a Reverse Osmosis Unit Reduces Refinery Energy Consumption (PDF) (4pp, 225K)
- Energy-Saving Separation Technology for the Petroleum Industry (PDF) (2pp, 112K)
- Advanced Process Analysis for Petroleum Refining (PDF) (2pp, 1M)
- Fouling Minimization (PDF) (2pp, 1M)
Get Recognition
Are you using water and energy efficiently? EPA would like to recognize your important contribution! The Water Efficiency Leader Awards recognize organizations and individuals for their leadership and innovation in water efficient products and practices. ENERGY STAR’s Partner of the Year Awards recognize partners’ special achievements in transforming their markets to ENERGY STAR. EPA presents these awards at the annual ENERGY STAR Awards banquet and reception in Washington D.C.