Center for Corporate Climate Leadership Sector Spotlight: Electronics
EPA is seeking to highlight activities to reduce supply chain greenhouse gas (GHG) emissions at the sectoral level. As a first initiative, EPA is featuring the electronics sector, specifically flat panel display suppliers' efforts to reduce F-GHG emissions in flat panel manufacturing.
On this page:
- Electronics: Flat Panel Display Manufacturing
- F-GHG Emissions Reduction Efforts: Flat Panel Display Suppliers
- What are F-GHGs and How are They Used in Panel Manufacturing?
- Why is This a Priority?
- How Can F-GHGs be Reduced?
- Questions for Suppliers: Tools for Panel Purchasers and Retailers
- Background on EPA Efforts
- Additional Resources
Electronics: Flat Panel Display Manufacturing
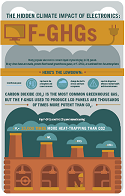

Starting in late 2013, brands and retailers Wal-Mart, Dell, HP, Lenovo, Best Buy and Acer took an important step to encourage further F-GHG reductions among their LCD suppliers by asking suppliers to develop a standard method for measuring F-GHG emissions, set new voluntary F-GHG emissions reduction goals with public timelines for demonstrating progress, and develop annual progress reports.
F-GHG Emissions Reduction Efforts: Flat Panel Display Suppliers
The Supplier Profiles detail the efforts of large-area flat panel suppliers to reduce their F-GHG emissions in manufacturing across key areas. They cover mitigation measures and goals, the extent of reduction efforts (whether they include all processes and gases used), the extent to which abatement technologies are installed on newer fabs that manufacture large area panels, and public disclosure efforts.
Most Current Supplier Profiles; Updates feature 2014 information
Previous Supplier Profiles; Features 2011, 2012, and 2013 information
- 2015 Summary of Supplier Profiles
- 2015 Supplier Profiles
- 2014 Summary of Supplier Profiles
- 2014 Supplier Profiles
- 2013 Summary of Supplier Profiles
- 2013 Supplier Profiles
In the News! Environmental Leader Articles:
- Major Companies Push LCD Suppliers to Make F-GHG Reductions. ExitJuly 30, 2014
- EPA Initiative Aims to Cut Suppliers' F-GHG Emissions. ExitSeptember 20, 2013
What are F-GHGs and How are They Used in Panel Manufacturing?
Fluorinated GHGs such as certain perfluorocarbons (e.g., CF4, C2F6, C4F8), trifluoromethane (CHF3), nitrogen trifluoride (NF3), and sulfur hexafluoride (SF6) are among the most potent greenhouse gases (GHGs), with some persisting in the atmosphere for thousands of years effectively causing irreversible impacts on the earth's climate system. These gases are commonly used in many types of electronics manufacturing, including the manufacture of flat panel displays, semiconductors, micro-electro-mechanical systems, light emitting diodes, and photovoltaic cells.
Flat panel display manufacturers—namely those that produce LCD panels used in products such as televisions, computer monitors, tablets, and mobile phones—use various F-GHGs and N2O during panel production. These gases, which are highly effective in their process performance, are used to etch intricate patterns onto the glass, during deposition, and to rapidly clean the chemical vapor deposition (CVD) tool chambers (see Table 1 for some of the process chemicals used by the industry and the environmental impact of the gases if released to atmosphere). Fluorinated heat transfer fluids are also used in the manufacture of flat panel displays to cool manufacturing equipment, for example, and can be emitted through evaporative
Compound | Application | Atmospheric Lifetime (years) | Global Warming Potential (100 year) | |
---|---|---|---|---|
CVD Chamber Cleaning | Plasma Etching | |||
CO2 | N/A | N/A | variable | 1 |
C2F6 | √ | √ | 10,000 | 12,200 |
CF4 | √ | 50,000 | 7,390 | |
SF6 | √ | √ | 3,200 | 22,800 |
NF3 | √ | √ | 740 | 17,200 |
CHF3 | √ | 270 | 11,700 | |
C3F8 | √ | 2,600 | 8,830 | |
c-C4F8 | √ | √ | 3,200 | 10,300 |
Source: IPCC, 2007 Exit |
During manufacturing of flat panel displays, a portion of F-GHGs pass through the manufacturing tool chambers unreacted and are released into the atmosphere (IPCC, 2006). A portion of the F-GHGs used in processes may also react in chambers to form by-product emissions, or emissions of other F-GHGs. The magnitude of emissions can vary depending on a number of factors including: gas used, type/brand of equipment used, company-specific process parameters, and number of F-GHG using steps in a production process. Companies' manufacturing processes and, consequently, emissions also vary across flat panel manufacturing fabs (i.e., manufacturing, or fabrication, facilities).
Why is This a Priority?
Over the last decade, major flat panel suppliers have taken voluntary steps to reduce their F-GHG emissions. For example, in 2001, the World LCD Industry Cooperation Committee (WLICC) (including the LCD industry associations in Korea (the Environment Association of LCD in Korea or EALCD/EDIRAK), Taiwan (Taiwan TFT-LCD Association or TTLA), and Japan (the Industries Research Committee in Japan or LIREC/JEITA)), agreed to voluntary reduction activities and set a goal to reduce F-GHG emissions to 0.82 MMTCE by 2010. They estimated that these reductions represented one tenth of their anticipated emissions, effectively reducing 2000 baseline levels by approximately 90 percent (WLICC calculated that F-GHG emissions in 2010 would reach 8.2 MMTCE without implementing any reduction measures) (Sources: Nishida, et al. PFC Emission Reduction Strategy for the LCD Industry. Journal of the SID 13/10. 2005 and WLICC Working Group 1 Activity Report on the 2012 FCs Reduction. World LCD Industry Cooperation Committee. November 10, 2011, Tokyo (PDF) (2 pp, 47K) Exit. To meet the reduction goal, many suppliers in participating countries implemented strategies to address their emissions including installing abatement technologies on production lines in their newer generation fabs, namely those built within the last decade. As a result, F-GHG emissions were reduced by 10.1 MMTCE, to where aggregate emissions totaled 1.75 MMTCE. Though these reductions demonstrated significant accomplishments, the WLICC fell short of its goal due to a rise in emissions resulting from a rapid increase in production for LCD panels that were integrated into products such as televisions faster than initially anticipated (Source: WLICC Working Group 1 Activity Report on the 2012 FCs Reduction. World LCD Industry Cooperation Committee. November 10, 2011, Tokyo (PDF)(2 pp, 47K) Exit.
Since the WLICC set its goals, newer suppliers with growing market share—those who have not participated in the WLICC's F-GHG reduction efforts to date—have also emerged and information on their F-GHG emissions reductions efforts is currently unknown. In addition, it appears that some key suppliers are still in varying stages of implementing comprehensive F-GHG emission reductions efforts across their fabs. As worldwide demand for flat panels, namely LCDs, continue to increase, F-GHG emissions are also projected to rise. To mitigate those emissions, it is important that reduction efforts across all major panel suppliers are implemented.
How Can F-GHGs be Reduced?
Over the last decade, electronics manufacturers have made significant progress in identifying effective technological solutions to reducing F-GHG emissions. The following approaches to reducing F-GHG emissions resulting from flat panel manufacturing are in use today or are currently being explored:
- Process improvements/source reduction: Manufacturers optimize their processes to use F-GHGs more efficiently, especially in the chemical vapor deposition clean processes, resulting in smaller amounts of gas that are unreacted and emitted.
- Alternative chemicals: Manufacturers use alternative lower Global Warming Potential (GWP) or more efficient gases to accomplish the same result. In the case of chemical vapor deposition (CVD) remote plasma chamber cleaning, many manufacturers have modified their processes to be able to use NF3 instead of SF6. Though NF3 still has very high GWP, it is lower than that of SF6. Some companies are piloting the use of F2 to replace NF3 in the remote plasma chamber cleaning process, seeking to surmount some of the challenges associated with transport, storage, and use.
- Capture and beneficial reuse: Manufacturers capture F-GHGs and process them to remove impurities and refine them for reuse. Some suppliers are evaluating the opportunities; reuse/recycling has so far not been implemented widely due to limitations on the effectiveness and cost of available technologies.
- Abatement via gas destruction technologies: Both point-of-use abatement, where the abatement system is attached to tools, and centralized abatement systems, where gases are sent to, and destroyed in, a centralized system, are being used by major panel suppliers. The majority of abatement systems in use are combustion-based. Though suppliers employ a mix of strategies to reduce F-GHGs, abatement remains one of the most effective ways to reduce the majority of F-GHG emissions.
Measuring the efficiency of an installed abatement system to destroy or remove gases such as F-GHGs—known as the destruction or removal efficiency (DRE)—directly relates to how suppliers can account for their annual F-GHG emissions and subsequent reductions. Most suppliers today use default factors from the 2006 IPCC Guidelines to account for the DRE of abatement systems. However, suppliers may also directly measure DREs using measurement guidelines or protocols. An example of such a protocol is the United States Environmental Protection Agency's "Protocol for Measuring Destruction or Removal Efficiency (DRE) of Fluorinated Greenhouse Gas Abatement Equipment in Electronics Manufacturing" (EPA's DRE Protocol). Published in 2010 and internationally peer-reviewed, EPA's DRE Protocol provides a reliable method for measuring DRE's of point-of-use abatement systems for F-GHGs used during the manufacture of electronics. In other cases, suppliers may monitor their systems on an ongoing basis, especially in the case of Clean Development Mechanism (CDM) projects, to acquire on-site real-time data. Suppliers may also test their abatement systems by monitoring specific parameters such as temperature, process gas, and exhaust gas flow rate. Going forward, EPA anticipates that additional information on industry practices can highlight which DRE measurement approaches are being used throughout the industry to produce reliable estimates of abatement systems' DREs.
Questions for Suppliers: Tools for Panel Purchasers and Retailers
Product assemblers/brands and retailers can play an important role in reducing the climate impacts of the products they sell by sourcing from suppliers with a demonstrated commitment to reducing F-GHG emissions.
It is important to note that currently it is difficult and unadvisable to try to compare panel suppliers' F-GHG emissions due to a lack of consistency in estimating emissions, estimating emissions reductions, and monitoring the efficacy of installed abatement systems. Therefore, the following sets of questions are intended to be a starting point to help customers understand how their panel suppliers are reducing their F-GHG emissions and identify opportunities for discussions to target and implement further mitigation efforts.
Background on EPA Efforts
For more than twenty years, EPA has worked collaboratively with the high-tech electronics industry to identify strategies for reducing greenhouse gas emissions resulting from its operations and from the products it creates for consumers.
- From 1996 to 2010, EPA's Perfluorinated Carbon (PFC) Reduction/Climate Partnership for the Semiconductor Industry supported and helped facilitate the industry's voluntary efforts to reduce emissions of F-GHGs. In 1999, Partners voluntarily committed to reducing F-GHG emissions by at least 10 percent below a 1995 baseline. To this end, EPA worked with the industry to identify, evaluate, and implement new technologies to mitigate F-GHG emissions. As a result, industry Partners reduced emissions by more than 50 percent below the 1995 baseline, or by a little more than 2 million metric tons of CO2e. This reduction is equivalent to the energy used in approximately 103,000 homes per year.
- From 2002-2010, EPA worked with various companies in the electronics sector to help them inventory their corporate-wide GHG emissions and set and achieve aggressive emissions reduction goals through identifying best practices. EPA continues to engage companies throughout the electronics industry on promoting the use of renewable energy through its Green Power Partnership, where companies such as Intel, Dell, Best Buy, and Microsoft rank among the top 50 leading Green Power Partners within the United States for their green power procurement.
- For more than 20 years, the ENERGY STAR program and its 16,000 partners have cumulatively prevented more than 2.1 billion metric tons of greenhouse gas emissions. ENERGY STAR-qualified IT and consumer electronic products continue to represent significant energy savings for the consumer. For example, televisions that meet today's ENERGY STAR requirements will eventually save American viewers and gamers over $700 million in energy costs, and reduce annual greenhouse gas emissions equivalent to that of nearly 900,000 cars annually.
Additional Resources
- EICC: Assessing and Reducing F-GHGs in the Electronics Supply Chain (March 2016) Exit(PDF, 7 pp, 1000K)
- EPA: PFC Reduction / Climate Partnership for the Semiconductor Industry
- JEITA: WLICC WG1 Activity Report on the 2010 FCs Emissions Reduction Exit(PDF, 2 pp, 48K)