Advanced Refrigeration
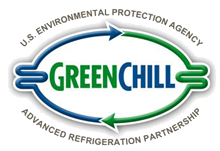
Most of the 35,000+ supermarkets in the United States use centralized direct expansion (DX) systems to chill their products. Typically, these refrigeration systems are charged with 3000 – 4000 pounds of refrigerant and can leak in excess of twenty percent of their charge each year. Commonly used refrigerants include ozone-depleting hydrochlorofluorocarbon (HCFC) refrigerants, often HCFC-22, and blends consisting entirely or primarily of hydrofluorocarbons (HFCs), both of which are potent greenhouse gases. Fortunately, in recent years there have been several advancements in refrigeration technology that can help food retailers reduce both refrigerant charges and refrigerant emissions.
Below is a general description of a centralized DX system as well as an overview of the different advanced refrigeration options.
On this page:
Centralized Direct Expansion System
At least 70 percent of stores in the United States use centralized DX systems to cool their display cases and walk-ins. In a DX system, the compressors are mounted together and share suction and discharge refrigeration lines that run throughout the store, feeding refrigerant to the cases and coolers. The compressors are located in a separate machine room, either in the back of the store or on its roof, to reduce noise and prevent customer access, while the condensers are usually air-cooled and hence are placed outside to reject heat.
The multiple compressor racks operate at various suction pressures to support display cases operating at different temperatures. The hot gas from the compressors is piped to the condenser and converted to liquid. The liquid refrigerant is then piped to the receiver and distributed to the cases and coolers by the liquid manifold. After cycling through the cases, the refrigerant returns to the suction manifold and the compressors.
Supermarkets tend to have one DX system for low-temperature refrigeration (e.g., ice cream, frozen foods, etc.) and one or two DX systems for medium-temperature refrigeration (e.g., meat, prepared foods, dairy, refrigerated drinks, etc.).
Schematic of a Centralized DX System
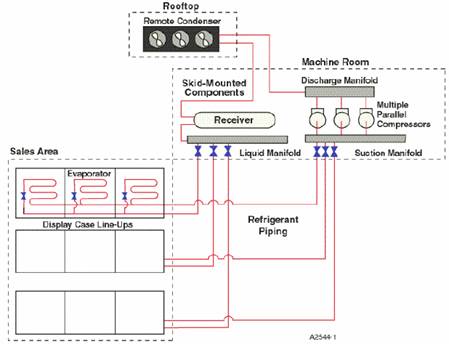
Source: International Energy Agency (IEA). 2003. "IEA Annex 26: Advanced Supermarket Refrigeration/Heat Recovery Systems, Final Report Volume 1-Executive Summary."
Distributed System
Unlike centralized direct expansion refrigeration systems, distributed systems use multiple smaller units that are located close to the display cases that they serve. For instance, compressors in a distributed system may be located on the roof above the cases, behind a nearby wall, or even on top of or next to the case in the sales area. The close proximity of the compressors to the cases and coolers allows the system to use considerably less piping and additionally use a smaller refrigerant charge than traditional DX systems. This reduction in charge often results in a decrease in total refrigerant emissions.
Schematic of a Distributed System
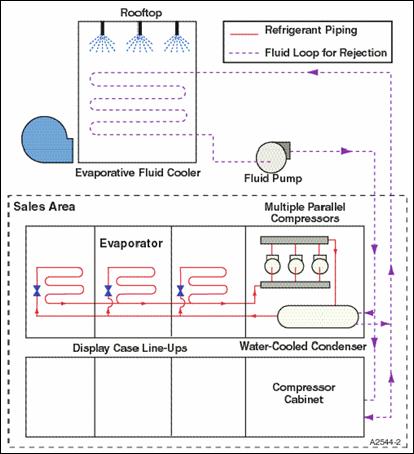
Source: International Energy Agency (IEA). 2003. "IEA Annex 26: Advanced Supermarket Refrigeration/Heat Recovery Systems, Final Report Volume 1-Executive Summary."
Secondary Loop System
Secondary loop systems use a much smaller refrigerant charge than traditional direct expansion refrigeration systems, and hence have significantly decreased total refrigerant emissions. In secondary loop systems, two liquids are used; a primary refrigerant and a secondary fluid. The secondary fluid is cooled by the primary refrigerant in the machine room and then pumped throughout the store to remove heat from the display equipment. Secondary loop systems typically ate with two to four chiller systems depending on the temperatures needed for the display cases.
Schematic of a Secondary Loop System
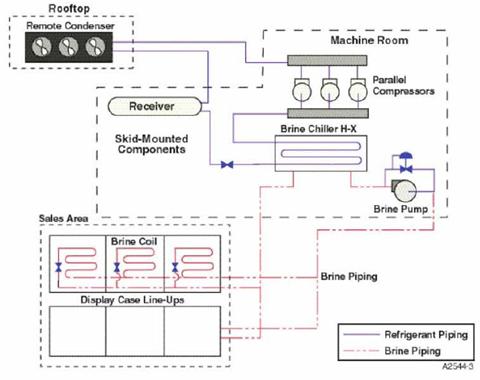
Source: Southern California Edison and Foster-Miller, Inc. 2004. "Investigation of Secondary Loop Supermarket Refrigeration Systems." Report prepared for California Energy Commission, Public Interest Energy Research Program.
Cascade System
Cascade systems consist of two independent refrigeration systems that share a common cascade heat exchanger. Each system of a cascade system uses a different refrigerant that is most suitable for the given temperature range. High temperature system uses high boiling point refrigerants such as R-404A, R-507A, R-134A, propane, butane, and ammonia, whereas low temperature systems use low boiling refrigerants such as R-744 (CO2) and R-508B. The advantages of a cascade system include a reduction in the refrigerant charge and a reduced carbon footprint.
Low-GWP Refrigerants
Similar to advanced refrigeration technologies, low-GWP refrigerants can also reduce the climate impacts of supermarket refrigeration systems. Refrigerants such as carbon dioxide (CO2), ammonia, hydrocarbons, and hydrofluoro-olefins (HFOs) have potential to be used in commercial refrigeration systems in the U.S. market. Currently only CO2 is being used as a primary refrigerant in commercial refrigeration system applications in the United States. Refrigeration systems that use CO2 as a primary refrigerant are commonly referred to as transcritical CO2 systems. Transcritical CO2 refrigeration is a type of refrigeration cycle in which CO2 is the sole refrigerant, evaporating in the subcritical region and rejecting heat at temperatures above the critical point in a gas cooler instead of a condenser. For more information on acceptable low-GWP refrigerants, see Acceptable Substitutes in Retail Food Refrigeration.